Our Expertise
Design Build
Shoring or Geostructural engineering involves the collective expertise of geotechnical, structural, and construction disciplines to analyze the intricate interactions among water, earth, and structures. Maple Site Solutions Inc. collaborates with highly experienced engineers who have extensive geostructural and shoring design experience. Some of these designs include (but are not limited to) secant and tangent pile walls, soldier piles and lagging walls, sheetpile walls, shotcrete walls, walls braced with tieback anchors (soil & rock), rakers, struts, etc. Our engineers’ primary focus is to provide optimized solutions that adhere strongly to the relevant design standards, but also consider clients’ constraints, particularly around geotechnical conditions. Emphasis is placed on achieving efficiency in design by optimizing safety factors and available construction material.
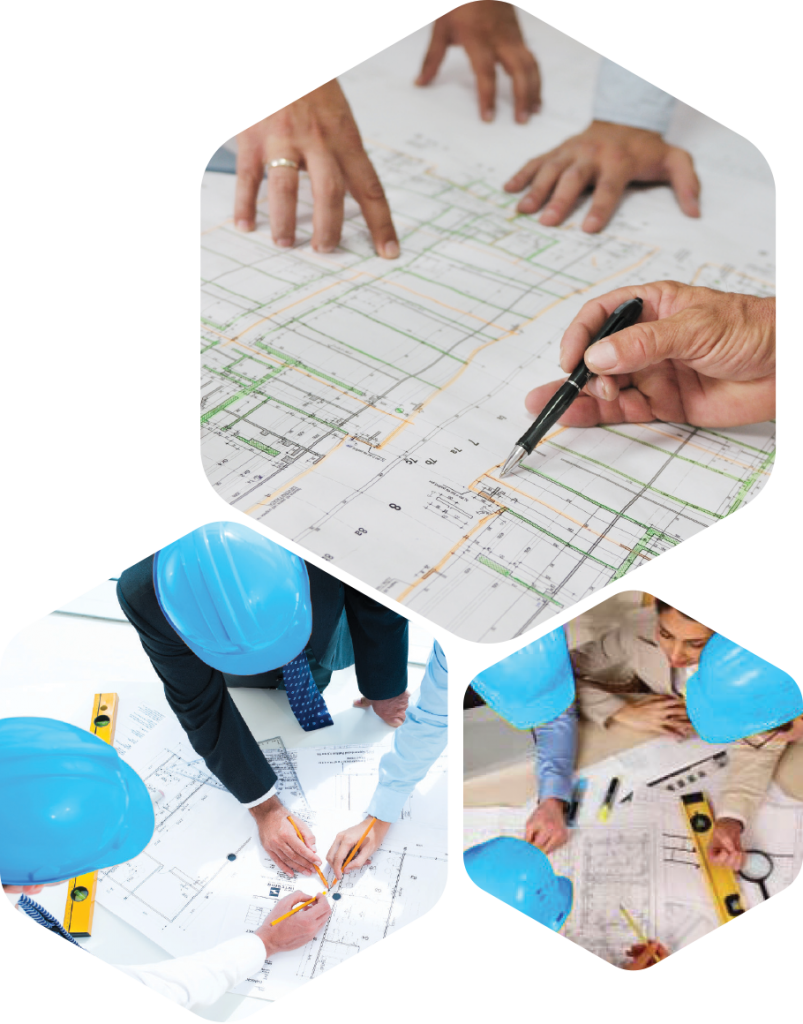
Shoring Types
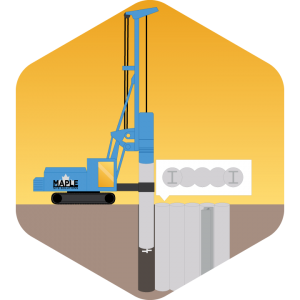
Caisson Walls
Caisson Walls (also known as secant walls) are interlocking bored concrete piles consisting of King Piles and Filler Piles. A King Pile is typically a structural wide flange steel member set in a bored hole filled with concrete, and the filler pile is a bored hole filled with just concrete. In some cases (not often), a king pile may use a reinforced steel cage in lieu of a structural wide flange steel member. A GeoStructural Engineer will determine king pile spacing, size, depth and king pile to filler pile geometry based on loads and pressures outlined in a geotechnical report.
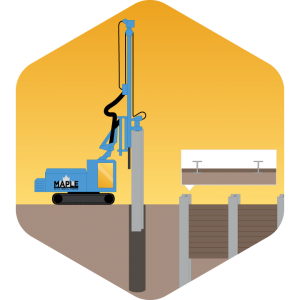
Piles and Lagging
Piles and Lagging is an intermittently spaced pile (a structural wide flange steel member set in a bored hole filled with concrete) with rough cut lumber spanning between piles behind the flange. The lagging is installed in lifts 1.2 -1.5m high depending on soil conditions as the excavation progresses.
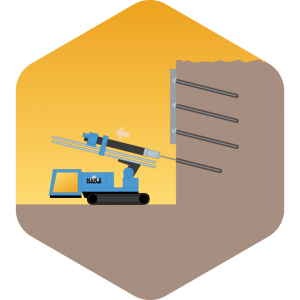
Shotcrete Shoring
Shotcrete Shoring (soil nailing) is a way of reinforcing blocks and wedges of soils utilizing earth anchors (tiebacks). Once the soil is reinforced (typically in lifts of 1.2 -1.5m high depending on soil conditions), all the earth anchors are tied together with welded wire mesh and concrete (Gunite). Concrete is placed using high pressure pumps and hoses directly at the wall face to ensure a void-less application from the finished face of shoring and soil (similar to pool construction).
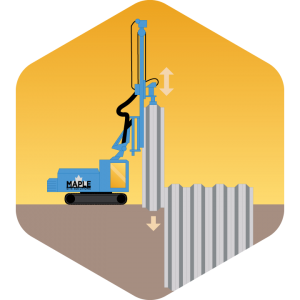
Sheet Piling
Sheet Piling is a structurally engineered interlocking sheet metal system (similar to corrugated metal), designed to be driven or vibrated into the ground. This system is typically used where vibration issues are not a concern, and to cut off ground water to create a cofferdam.
Shoring Bracing Methods
As depths and loads increase on shoring systems, bracing will be required for economic and constructability reasons. Selection of the bracing system is determined by restrictions such as tieback encroachments (drilling onto neighbouring properties), or watertight requirements of permanent structures.
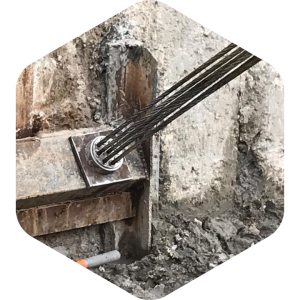
Tiebacks
Tiebacks (soil/ rock anchors) are small diameter diagonally drilled and grouted anchoring systems reinforced with a bar or multi-strand anchoring system. This system is designed at critical deflection points determined by a Geostructural Engineer. These anchors once installed, are tied into the main structural shoring elements and are tested and stressed to ensure and/or mitigate movement in a shoring system.
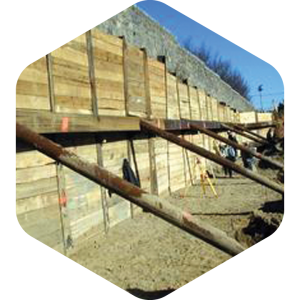
Rakers
Rakers are internally braced structural steel members (wide flange, HP section or hollow structural tube) diagonally braced from a critical deflection point of the shoring system inwards towards the excavation set into a concrete pad/foundation, also known as a raker pad.
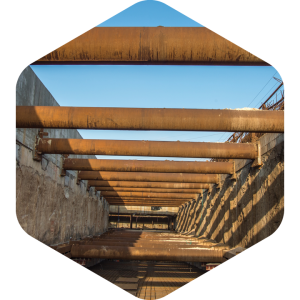
Struts
Struts are internally braced structural steel members (wide flange, HP section or hollow structural tube) horizontally braced members, placed at critical deflection points across the excavation where practical.
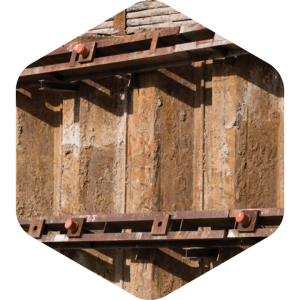
Walers
Walers are structural steel members (wide flange or HP section) that tie vertical shoring members (piles) together to distribute the loads and to prevent rotation of vertical members. Walers are installed (welded) continuously along the top or face of the piles and even in between for tieback applications
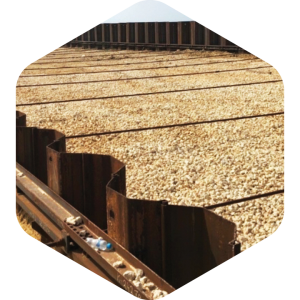
Deadman
Deadman is a support system behind the shoring that can be accessed conventionally through excavation and a mass pour of concrete can be delivered. The anchoring system can be done using anchors or structural steel members trenched from the critical point of the shoring and the concrete block.
FOUNDATION TYPES
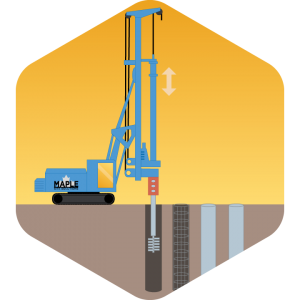
Caissons
Caissons (also known as bored concrete piles) are earth bored holes filled with structural concrete and rebar cages placed in the centre of the hole. This method is used when excavation depths to practical and adequate bearing capacity conditions cannot be met at the proposed underside of foundation levels. Caissons can be tied together with grade beams, pile caps or raft slabs. Caisson sizes vary from 450mm – 3000mm in diameter and typically increase in 150mm increments.
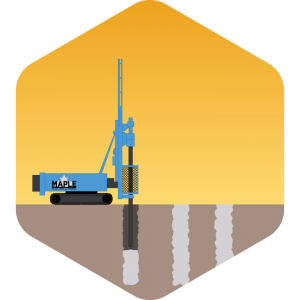
Micro-Piles
Micro-piles (also known as mini piles) are small diameter piles that support vertical loads in tight access locations where conventional caisson drilling is not practical, or in low headroom situations inside an existing building or structure.
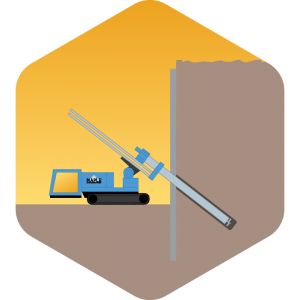
Soil Anchors
Soil and rock anchors are similar to micro-piles except they are typically used to resist uplift loads. Although these anchors are utilized for shoring, these members are typically installed vertically to hold down a structure in hydrostatic or buoyant conditions.
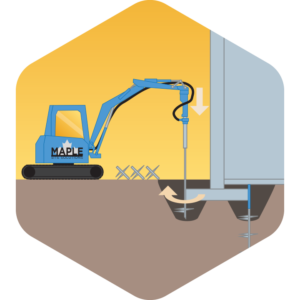
Helical Piles
Helical Piles (also known as screw piles) are engineered structural members with welded flights used to screw into soil. This system can be used for foundation support or tie down for hydrostatic or buoyant conditions. This system does not rely on any removal of spoils generated by other drilling methods and eliminates waiting time for concrete or grout to set.
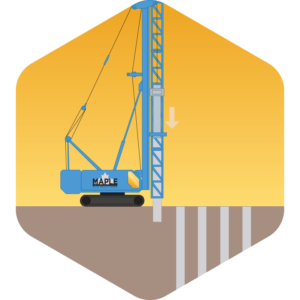
Driven Piles
Driven piles are deep foundation elements that provide structural support as well as lateral support for retaining walls. They are installed using impact or vibration hammers to a pre-determined depth or resistance. Driven piles can be installed in sequence as they do not create spoil, which eliminates waiting time for concrete or grout to set and speeds up production time.